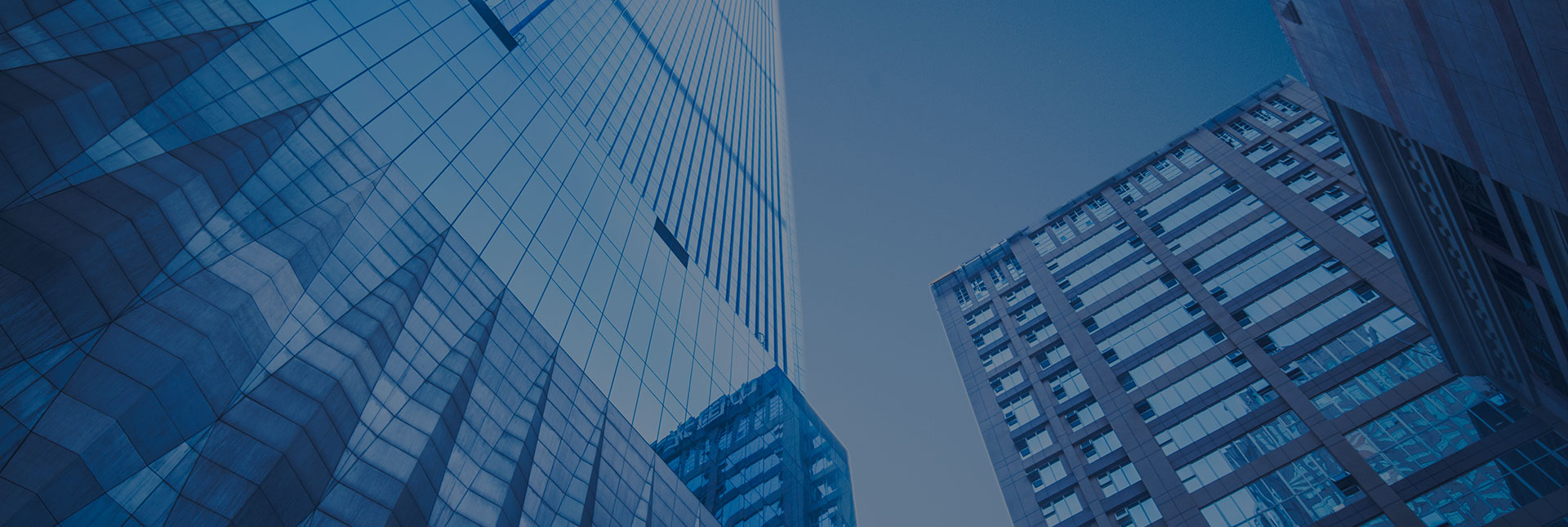
A wearable camera is installed or worn above the operation area. The camera will continuously collect visual images of the operation and transmit them to the AI terminal, and the AI module will identify the screw model and position of the received images; if the current screw model or position is found to be wrong, an intelligent warning will be given, displaying invalid torque output and warning messages; the user must make adjustments before continuing the operation.
The motor torque is estimated by a certain algorithm to calculate a more accurate current torque of the motor, and the torque is controlled in closed loop. The dynamic torque sensor is integrated in the bottom of the screwdriver to collect the output torque value during the operation. The collected torque value is compared with the set value in real time, and once the set value is exceeded, the motor power output will be shut down, and the digital display will send an alarm signal and display an error message in the system. The user loosens the screw and retightens it according to the prompt message.
This product adopts artificial intelligence technology, which allows users to remotely define the job content, remotely configure the parameters of the screwdriver, remotely monitor the operation of the screwdriver, and analyze the operation data through the system according to MPI requirements, thus promoting the quality control of the product. By breaking the barrier between software and hardware, the two can be integrated faster, thus saving manpower and time and improving the efficiency of enterprises.
The torque of the screwdriver is calibrated by the torque sensor, and the error accuracy of the torque loop is monitored in time according to the historical data of torque control and closed-loop comparison data; once the control accuracy exceeds the requirement an intelligent warning will be made to prompt the user to calibrate the torque. The user will fix the screwdriver on the specified screw, and the screwdriver will be automatically calibrated for accuracy, which improves work efficiency and saves manpower.
Based on the scenario design of Industrial Internet of Things, data transmission using MQTT and MES system; through the collection of equipment data, analysis of the latest data mastered in real time, data analysis, to achieve process and standardized management of work tasks; thus significantly increasing manufacturing efficiency, improving product quality, reducing product costs and resource consumption, and ultimately achieving the upgrading of traditional industry to a new stage of intelligence.
Function | Lite version | Flagship Edition | Robotic arm version | Automatic feeding plate | Super Edition |
Visual anti-dumbing of operation sequence | √ | √ | √ | √ | √ |
Software setting torque | √ | √ | √ | √ | √ |
Status signal light | √ | √ | √ | √ | √ |
Assignment Sequencing | √ | √ | √ | √ | √ |
Assignment visualization software | √ | √ | √ | √ | √ |
Screwdriver holder | √ | √ | √ | √ | √ |
Automatic calibration | √ | √ | √ | √ | √ |
Torque Tester | √ | √ | √ | √ | √ |
IoT Access | √ | √ | √ | √ | √ |
MES System Integration | √ | √ | √ | √ | √ |
Calibration Reminder | √ | √ | √ | √ | |
Torque closed loop control | √ | √ | √ | √ | |
Multi-axis robotic arm | √ | √ | √ | ||
Automatic feeder | √ | √ | |||
Robotic arm visual positioning | √ |
Total power:150w
Input Voltage:24V/DC
Width x Height x Thickness:0.25m*0.4m*0.15m
Length X Width X Thickness:55cm*32cm*8cm
Screen:24" resistive screen
Camera:Industrial camera 600W pixels
AI Controller:Embedded GPU
Network Interface:RJ45
Camera Interface:USB3.1
Power connection terminal:XT90 2pin
Torque sensor terminals:PHB 4pin
Motor terminals:PHB 9pin
Network Switches:1Gbps 5-port
Limit LED terminal:PHB 4pin
Operating temperature:0-60°C
Hight:45cm
Weight:450g
Batch head:1/4寸
Clamps: JT0
Torque range: 0.3~1.0 N.m
Diameter: 4.5cm
Housing material: PLA
Bracket grid height: 110cm
Arm length: 60cm